What is SAP A.T.T.P and what does it mean for the Pharma supply chain?
SAP ATTP, or rather SAP Advanced Track and Trace for Pharmaceutical, is a solution designed to support the new global legislation regarding tracking of pharmaceutical products. This legislation requires that medicine or medical equipment must be traceable and validated, which means manufacturers are responsible to prove that medicine is the original and authentic chemical it claims to be.
The problem:
“One pharmaceutical manufacturer reportedly discovered over 78 different counterfeit medications had infiltrated over 109 countries. That’s just one manufacturer. The problem is growing, with the World Health Organisation concerned that over 50% of online medications could be fake. Large numbers of medications are now produced in low-income countries. People are also shopping for medications online, and not paying attention to supply chains. This has led to substandard pharmaceuticals reaching patient markets around the world. Reports suggest from 10% to 70% of medications distributed internally in low-income countries are either counterfeit, contaminated or substandard.” (https://www.pharmout.net/counterfeit-medications-global-statistics/)
The solution:
Use technology to authenticate and logistically track everything, from the lowest unit such as a blister pack to the full pallets of goods distributed around the world. Know where everything is all the time. Introducing SAP A.T.T.P.
What are the components of SAP A.T.T.P ?
The SAP Advance Track and Trace for the Pharmaceutical industry comprises the following primary components:
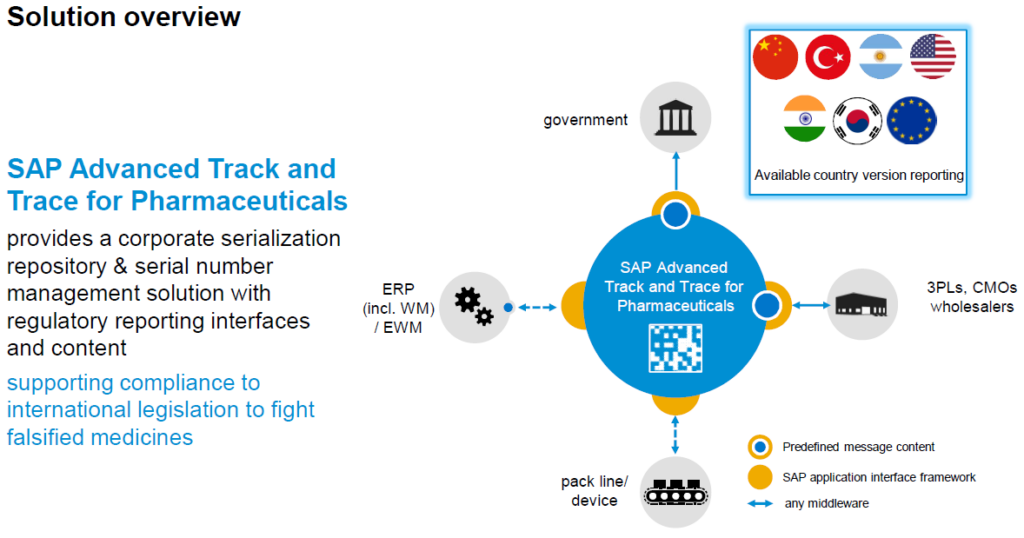
The solution or data repository is hosted by the original manufacturer and stores the origins of a serialised item. Once the serialised item is activated the system reports on the various activities (events) that are performed with the serialised item. Examples for these events are: The creation of the item, the dispatch of the item to the supply chain and the final usage of the item. All these events are stored in the SAP A.T.T.P system and reported to the governing body responsible for that logistically regulated area.
What is a serialised item and what is an event?
The complexity comes when we look at the makeup of a serialised item. The serial number itself is a unique number issued by the governing body to the original manufacturer of the item (This number range is unique for that manufacturer). The barcode format as well as the way the numbers and other information is stored in the barcode is defined by a strict international standard defined by the GS1 consortium. (https://www.gs1.org/)
Additionally, GS1 also defines the E.P.C.I.S standard (Electronic Product Code Information Services Standard). This standard enables disparate applications to create and share visibility using event data, both within and across enterprises. Basically, any system that would like to report an event, can report that event using the E.P.C.I.S message standard.
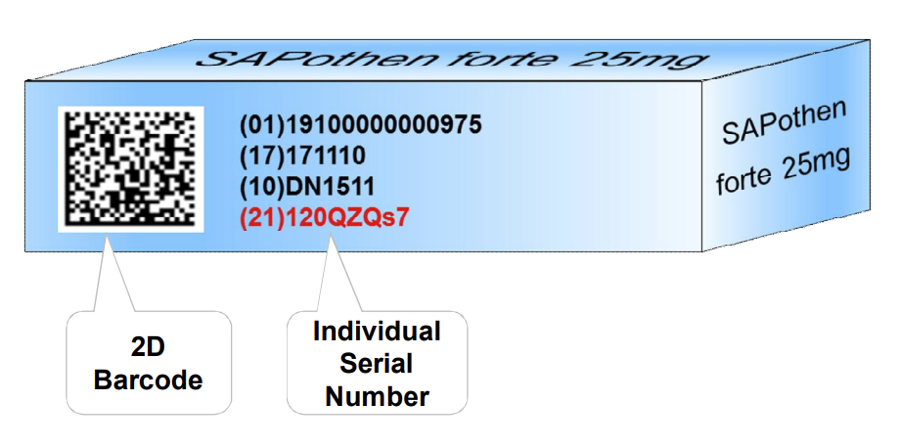
The GS1 standard defines how the serial number, as well as the other relevant information such as batch and shelf life, are captured in the barcode which is printed on the product to be tracked.
If everybody adheres to the standards, the barcode will be scannable by all manufacturers, distributors, and customer systems.

How does this tracking affect the supply chain?
If each unit has a unique serial number, would we have to scan each unit every time we move that unit? How does this affect stock take, stock receiving and shipping?
The most important place to start when implementing track and trace for the supply chain is that the correct GS1 standard and barcode format is used across the business. Then the next important aspect is the way a serialised item is created and activated.
If we look at the point where the serialised item enters the warehouse, it will more than likely be in the format of a full pallet or a packed pallet of goods or in packed cases.
Most commonly the case or the pallet is normally packed at the point of manufacture. It is at the stage that the capture of the new serial numbers and the building of what is called the aggregated package is done.
For example, the manufacturing process, when ready to package the goods, requests a valid serial number range from SAP A.T.T.P system. SAP A.T.T.P stores and manages the serial numbers that were issued by the standardisation body.
The A.T.T.P system then issues the serial numbers to the various manufacturing packaging lines; these packing lines print the barcode and serial number on the packaging. This is reported as successful after a validation scan by the packaging line and the SAP A.T.T.P system activates the serialised item and reports the activation to the governing body. (https://www.nmvs-connect.com/.)
Aggregation (packing the serial number children into parents) is typically done by an automated image capturing system that captures the barcodes and then aggregates them to the case (parent) serial number which in turn is then aggregated into the pallet serial number if the product is stored on pallets.
The pallet serial number will be the S.S.C.C (Serialised Shipping Container Code) number which is already a GS1 standard many companies are using. An S.S.C.C number range is also issued to companies to uniquely identify who is the owner of that pallet of stock.
Therefore, it is critical that manufacturers comply with the GS1 standard so that all companies agree on how goods are packed and shipped across the globe. In many instances, this is where track and trace systems find challenges, not all companies comply with GS1 standards globally.
If the stock has been activated and aggregated correctly from the manufacturing line, the master file or data bundle can be validated and distributed with track and trace.
If a partner company or member of the pharmaceutical community would like to validate a unit of medicine at any time, they are able to scan the serialised barcode and obtain the relevant information regarding that serialised item. How do items that have serial numbers affect the warehouse operation?
How do items that have serial numbers affect the warehouse operation?
Each business unit or logistics area in the business will be assigned what is known as a GLN (Global Location Number). When the warehouse receives a pallet of serialised stock, it updates the GLN for the pallet of stock. This information is sent to the global database.
The SAP logistics suite of products SAP ATTP, SAP ERP and SAP EWM are tightly integrated and support the tracking of serialised items. As events occur in the SAP EWM system, they are communicated to the SAP A.T.T.P solution automatically.
The SAP Advanced Trace and Trace solution provides its own mobile transactions supported by the Fiori platform. These mobile applications together with the embedded functionality that SAP EWM has in its mobile transactions allow the solution to update the trace and trace system with any events that might occur.
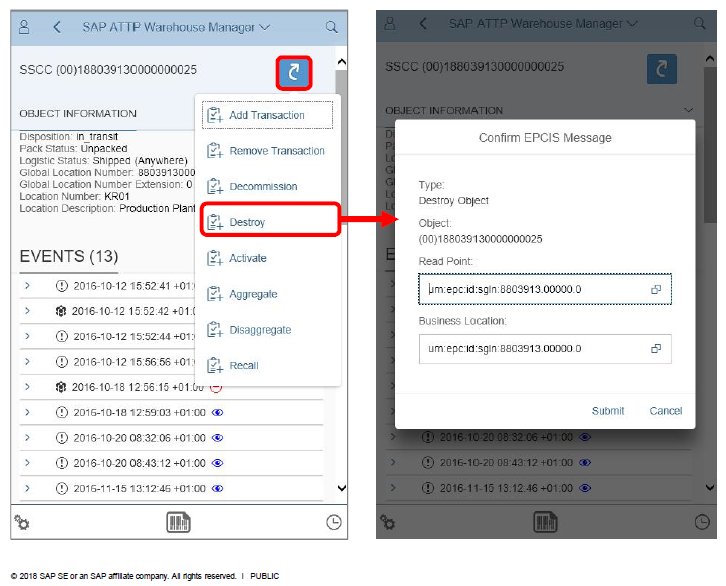
To the left is an example of the mobile transactions supported by the SAP A.T.T.P solution. This transaction can also be deployed at sites that are not running SAP or smaller sites such as doctors and pharmacies.
When the SAP Extended Warehouse Solution detects that a serialised pallet has arrived, it sends a location update event to the A.T.T.P database.
The primary advantage or using the SAP integration is that the warehouse is able to scan the parent (pallet) barcode and automatically the location of all the “child” serial numbers will be updated. This is a significant advantage as the warehouse would not have time to scan the serial number of each item, additionally no unpacking and relabelling is required if the outer packaging is intact.
This results in minimal impact on the warehouse resources. Only if a pallet has gone missing or is damaged, would the warehouse have to perform more track and trace transaction to determine which serial number has been damaged and must be de-activated from the track and trace solution.
Below is an example of the Advanced Trace and Trace mobile transaction validating that a serial number is valid. The application uses the mobile devices camera to decode the barcode, there is no need for special mobile devices or scanning functionality.
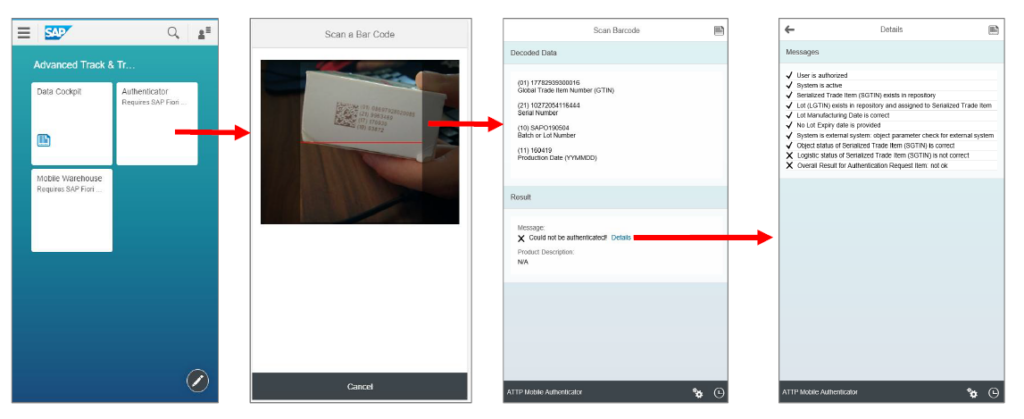
For stock take, the native integrated support for SAP A.T.T.P in the warehouser solution allows that missing serial number can be identified during stock take and the appropriate corrective action can take place.
During the dispatch process, the warehouse solution will automatically record the picked serial number and update the SAP A.T.T.P system that the picked unit has been dispatched. The customer information is also maintained on the ATTP system so that the intended recipient can be reported to the tracking system and then in turn to the governing body.
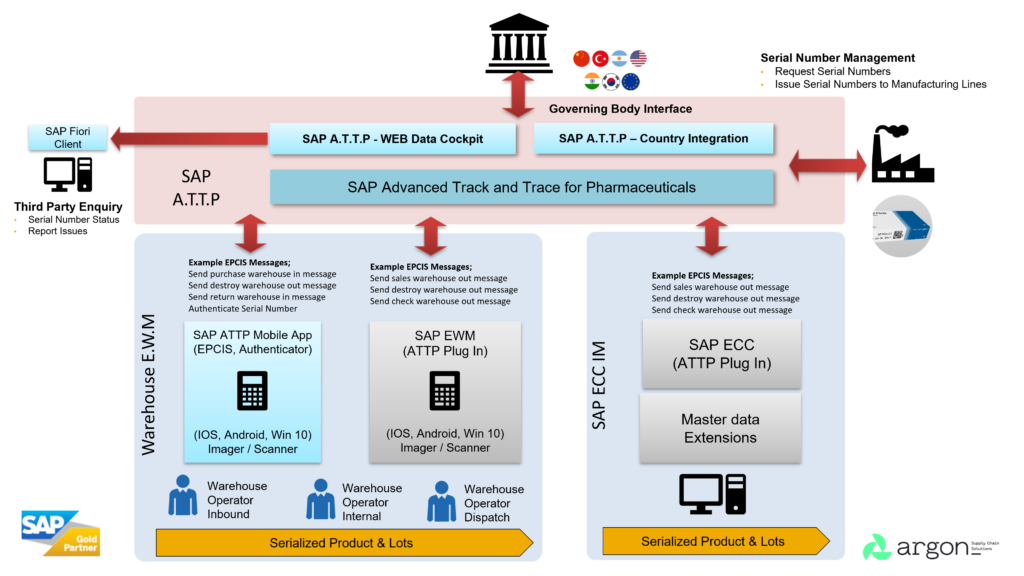
Summary: Medical forgery and the manufacturer of counterfeit goods is on the increase. The safety of all patients and the integrity of medicine must be protected. The adoption of advanced track and trace in the 3 rd world countries is lagging, the technology is available to track and control the flow of these important products.
References:
EPC Information Services (EPCIS) Standard – Release 1.2, Ratified, Sep 2016
SAP Advanced Track and Trace for Pharmaceuticals Solution Overview – Peer Laslo, SAP Services
December 03rd 2015
For more information, contact us info@argonscs.com.